Industrial Wedge Screen
Home » Our Products » Industrial Wedge Screen
V Wire Screen Pipe
V – Wire Screens are fabricated in Pipe Form from Wires. All Welded Wedge Wires Screen is made from two elements – Outside V-shape wire and Inside Longitudinal Rods.
The V-shaped Wire is spirally wrapped on a Cage made of Longitudinal Rods. The intersecting of shaped wire and rod is welded through each other by resistance welding. Due to resistance welding the weld joined is very strong.
“V-Wire Screen Filter” is a Highly Acceptable Modern Technology in Rain Water Harvesting. It eliminates conventional filtration systems, SAVES -Precious Space, Construction Cost, and Construction Time for Filtration Tank. Scientific Design helps Cleaning Very Easy and SAVES Maintenance Costs.
Features and Benefits of "V Wire Screen
- Cohesive Material : Made from Stainless Steel and Suitable for acid treatment to remove incrustation, and chocking of gravels which ENSURES the LONG LIFE of the bore well
- V Shaped Slot: Produces jetting effect to inject recharge water into the aquifer.
- Continuous Slots Give Large % Open Area
- Easy Installation: Save Money, Time, and Energy Customized for very small or large rooftop areas.
Technical Details
- Slot size 0.15 mm to 10 mm
- Length 0.2 mtr – 6 mtr.
- Material – SS 304/316/316 L or LCG or as per Customer Requirement
- End fittings – as per customer requirement.
a call to action
talk to us today!

Rotary Screen
Rotary wedge wire screens remove solids and other debris from the wastewater stream to protect downstream equipment such as pumps and irrigation nozzles. The screens are suitable for all types of wastewater. The solid screening is discharged by gravity. The screens are employed at chemical plants, papers and pulps, dairy farms, and food processors. They are designed to minimize obstructions, maintenance, and power consumption.
Rotary wedge wire screen operation: Wastewater enters the wire and is evenly distributed on the side walls of the drum. The solids are retained on the screen surface and the liquid flows through the screen holes. The solids are transported by flights at the open end of the drum. The rotation of the drum allows the entire screening surface to be continuously washed with wastewater. Cleaning is also achieved by intermittent use of an external spray nozzle.
Rotary Wedge Wire Screen Options
- Materials of construction – SS AISI 430, 201, 202,304, 304L, 316, 316L,
- Aperture range – 0.05-10mm.
- Sizes: Ø100mm – Ø2500mm & Length up to 6.5 Mtr.
Rotary Wedge Wire Screens Feature
- In-feed flow distribution weir – Screen element of 304 stainless steel construction with screen size to suit flow and chosen screen aperture.
Run Down Screen
We have developed complete run-down screens (DSM type) with box and curved wedge wire screens to suit specific customer requirements in the sugar, paper pulp, water treatment, and chemical industries.
A no-moving part unit that cascades a solids-laden slurry down a wedge wire screen to separate solids from liquids. The slurry is pumped or gravity-fed into the top chamber of the unit, flows over the full-width wires, and cascades down the curved screen surface. The liquid passes through the screen voids into the collection chamber below. Solid particles larger than the screen void size remain on the surface, and as this accumulating mass increases in weight/volume, it gently slides down the screen surface, compacting and becoming more water-rich as it goes down. At the bottom discharge chute, the solids simply fall off or, in some applications, go through a drum or screw press unit for further dewatering. The static screen version has its screen rigidly fixed in position while another, more efficient unit, is mounted to enable a small motor to vibrate its screen.
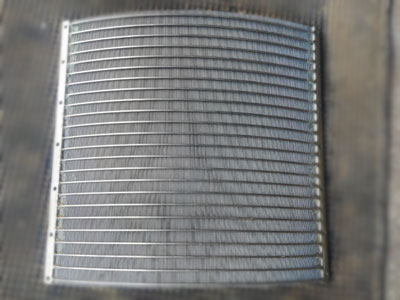
Options Available
- Front or rear spray bars
- Swivel screens for ease of cleaning
- Screen slot (Aperture) sizes: 0.05mm to 10mm
- Material of Construction: SS AISI 430, 201, 202, 304, 304L, 316, 316L.
Feature Of Run Down Screen
- 304 stainless steel construction
- Housing in 3 mm thick plate
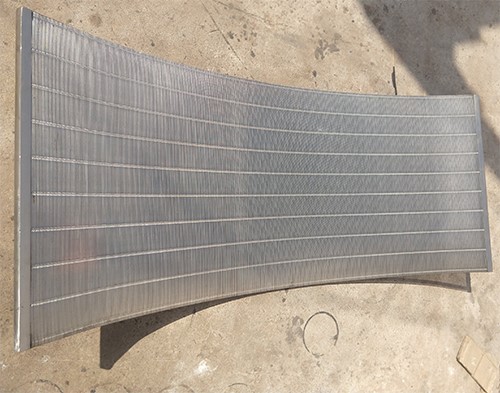
Water Fall Screens
When you need the most effective method for solids removal, trust our ClearBlu wedge wire waterfall system.
Wedge wire waterfall screens offer a highly efficient and cost-effective alternative to other solids removal systems. Several factors make this wedge wire screen an excellent choice.
wedge wire screen
- The wedge wire screens have a very steep angle. This allows water flow to push screened material off into a dewatering hopper.
- 5 mm screens will actually separate material as small as .25 mm.
- Automatic spray bars keep dried material from clogging the wedge wire screens. Because they are timer-activated, they use 90% less water than rotary screens.
- Stainless steel construction means acidic wastewater is no challenge.
- Screening solids before pH balancing can reduce chemical consumption by 60%. Solids can soak up significant amounts of the chemical.
Applications
- Wineries
- Breweries
- Food Processors
- Agricultural
- Industrial (garbage companies, municipal yards, etc)